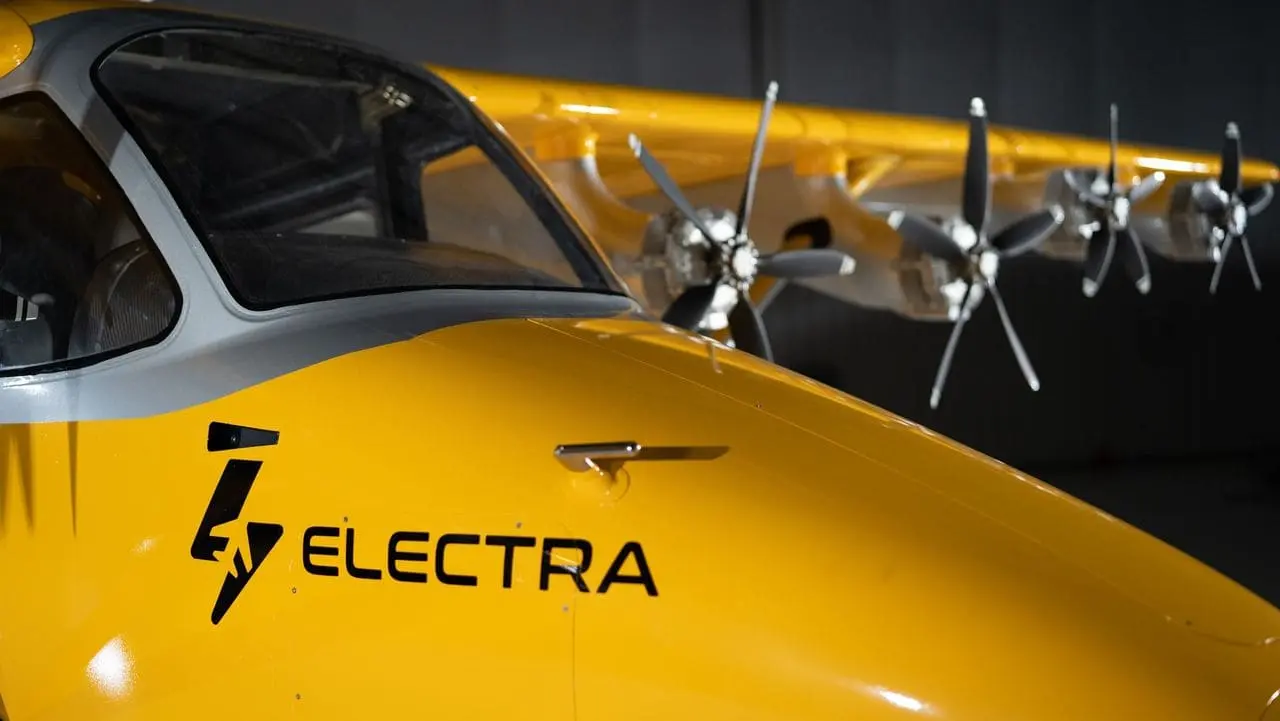
Harnessing electric propulsion
for breakthrough performance
Our Ultra Short aircraft uses eight electric motors placed along the leading edge of the wing, resulting in a dramatic improvement in aerodynamic performance. This innovative design enables our aircraft to achieve ultra-short takeoff performance and maintain a low noise footprint. Coupled with our hybrid-electric propulsion system, the Ultra Short consumes significantly less fuel compared to conventional aircraft. Fly-by-wire flight controls ensure precise landings, even in tight spaces.
Blown-Lift
Enhanced aerodynamic performance for compact operations
By blowing air over the wing and large flaps with an array of electric motors, our Ultra Short aircraft multiplies the amount of lift the wing makes at very slow speeds. With this technique, we can take off and land at speeds as slow as 35 knots, which only takes a few vehicle lengths to achieve. The key is in the accelerated airflow forming a thick jet sheet coming off of the trailing edge of the wing, making the wing act virtually larger than it physically is. In climb and cruise, we reduce blowing and stow the flaps for ultra-efficient operations.
Hybrid-Electric
Propulsion
All-electric power.
Hybrid-electric energy.
Our hybrid-electric propulsion system uses a combination of a turbogenerator and battery packs to power the aircraft's electric motors. The turbogenerator is sized for cruise, while the battery boosts power for takeoff and landing. This way, the turbogenerator can be small and always operates at its most efficient operating point.
This reduces fuel burn and lowers maintenance cost. Operators can choose to charge the battery in flight via the turbogenerator or re-charge on the ground where charging infrastructure is available. However, charging infrastructure is not required. The turbogenerator supports up to 100% sustainable aviation fuels and future use of eFuels or hydrogen for zero-emissions flight.
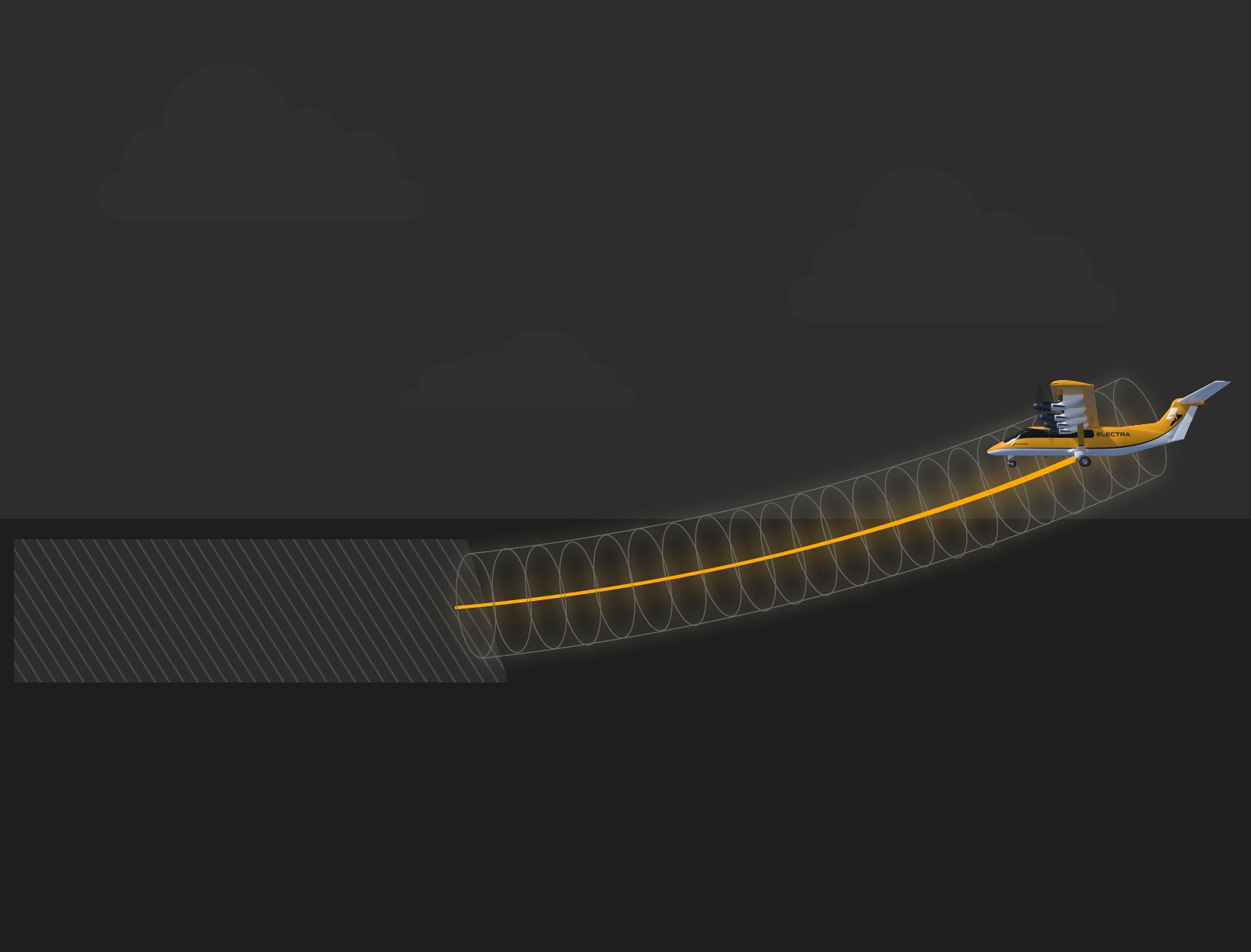
Fly-by-wire
Advanced flight controls for precision operations.
Our triplex redundant, fly-by-wire system automatically coordinates actuation of the flight control surfaces and eight electric motors to maintain safe operations throughout the flight. It automatically manages the complexity of operating in the slow-speed flight envelope to ensure repeatable precision landings, addressing past challenges with conventional designs.
Taking it to the next level
At Electra, we’re excited to lay the groundwork for technologies that have the potential to reduce emissions not just for small aircraft, but also for larger transport aircraft to decarbonize aviation on a greater scale. Hybrid-electric propulsion and smart integration of the electric propulsors with the airframe is one such technology. We are currently collaborating with the Massachusetts Institute of Technology, the University of Michigan, and industry partners to explore such future aircraft concepts.